Battery Day 2024: three innovative entrepreneurs on their sustainable battery solutions
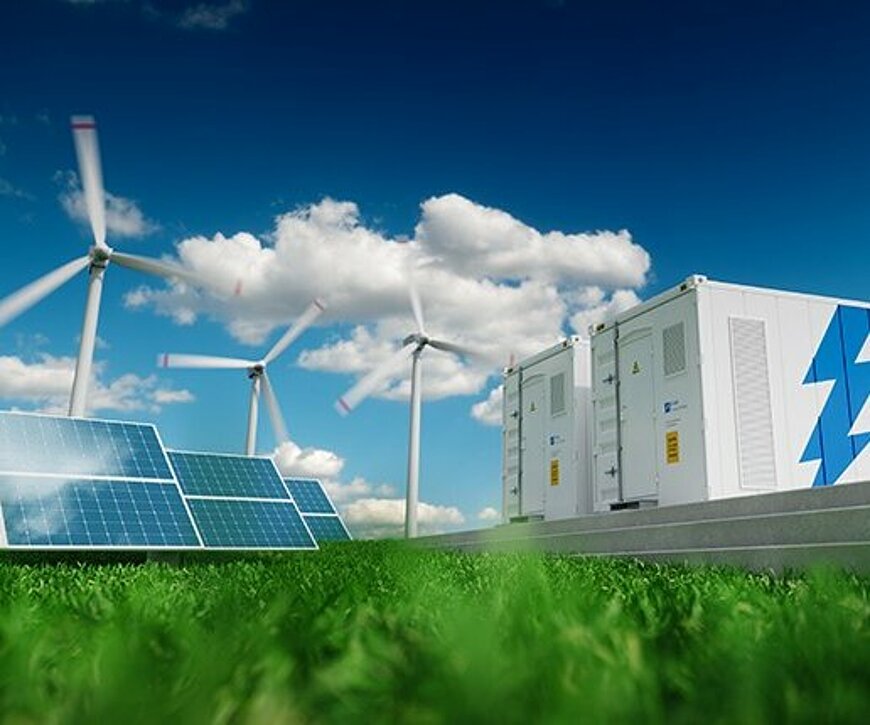
The Netherlands is a leader in batteries that efficiently store excess sustainable energy. By supporting innovative entrepreneurs, InnovationQuarter contributes to the development of the battery ecosystem. Three entrepreneurs talk about their innovation, ambitions and the importance of making a positive contribution to the energy transition.
F.l.t.r. Gijsbert Bakker (CEO Phoenix Metals), Rutger van Raalten (Co-founder CarbonX) and Diederick Spee (CEO Kalpana Systems)
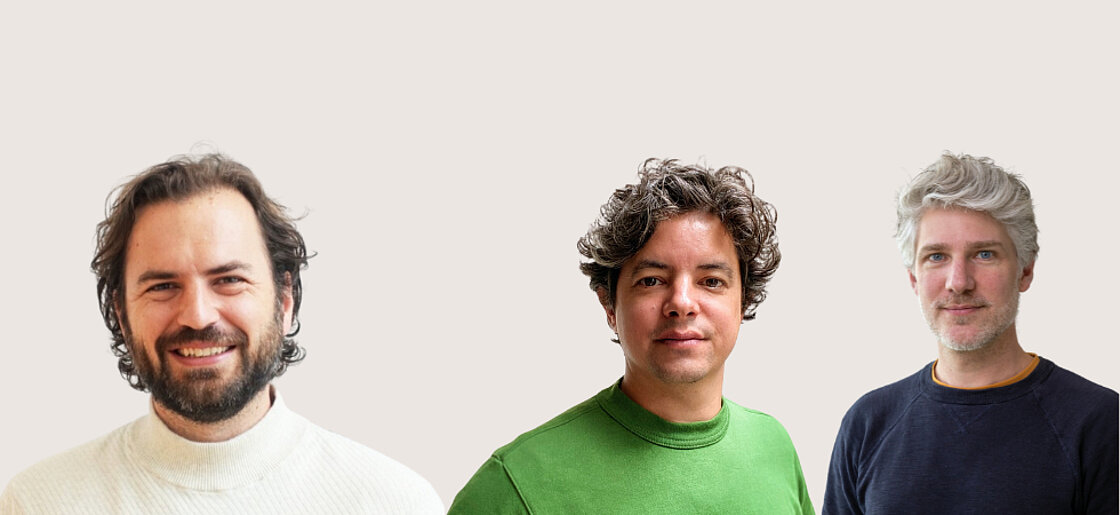
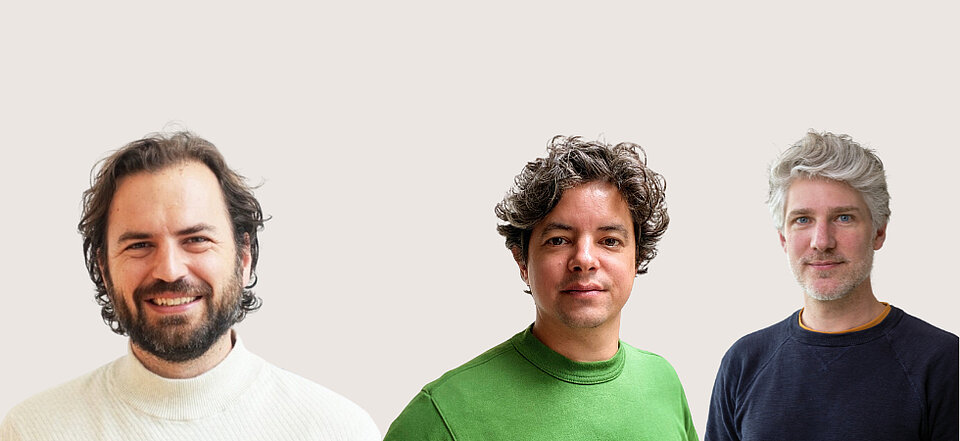
Phoenix Metals: industrial waste as raw material for batteries
CEO Gijsbert Bakker has always been interested in the circular economy. ‘I think engineers have an ethical responsibility to make their products circular and prevent overconsumption.’ And that is exactly what his company Phoenix Metals is doing. It produces vanadium electrolyte from industrial waste and residue streams for use in flow batteries. These batteries can be widely used for energy storage and to tackle grid congestion.
Sustainable battery production
New battery technologies are in high demand. Lithium-ion batteries, such as those used in phones and laptops, are not suitable for large-scale energy storage. Flow batteries, therefore, are, but require raw materials such as vanadium. 'What makes our innovation innovative is that we do not import vanadium from China, for example, but recover it from residual and waste streams in the Netherlands. The result is what we call ‘battery-grade vanadium’.' Gijsbert wants to commercialise his product through an energy-efficient extraction process. That process is sustainable; no organic solvents or ammonia are used, for example.
Proof of concept in Rotterdam port
To scale up, InnovationQuarter is helping the startup, among other things, by subsidising a proof of concept. Small batches of electrolyte will soon be produced in the Rotterdam port area to prove the technology. But the support is not only financial. 'Thanks to InnovationQuarter, we are part of a large ecosystem in the Netherlands. Their network, support and trust are indispensable. They contribute to our growth in multiple ways.'
‘I think engineers have an ethical responsibility to make their products circular and prevent overconsumption.’
Gijsbert Bakker, Phoenix Metals
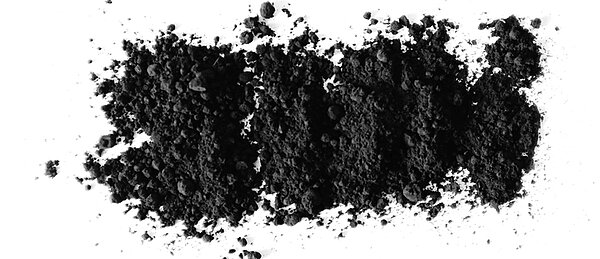
CarbonX: solution to graphite shortage in battery production
Rutger van Raalten, co-founder of CarbonX, began his career as an inventor at TU Delft. There, on an experimental Friday afternoon, he stupidly stumbled across an innovative carbon anode material. The material turned out to be a more durable, cheaper and more efficient alternative to graphite, with applications in car tyres and batteries, among others. For the latter, it also offers benefits such as faster charge times and improved stability. The material could play an important role in the energy transition and reduce dependence on China for graphite. Rutger founded CarbonX to develop it further, with university support.
Local production
InnovationQuarter helped CarbonX scale up the technology and increase production capacity. ‘As a regional investor, they felt it was important to bring production back to Europe.’ The close collaboration not only provides help in finding investors, but also gives access to regional expertise. 'InnovationQuarter thinks with us from day one. They understand what the landscape looks like. Not only in business, but also in government. You don't know that as a startup.' Indeed: ‘As a startup, you're not always taken seriously. But partly thanks to InnovationQuarter, we were soon able to compete with the big players.'
Expanding to Europe and the US
The ambition is to set up a large-scale production line in Europe, and later also in the US. In addition, CarbonX is developing a battery test lab in the Netherlands to support customers and further boost local production. 'Responding to the opportunities in front of you is what I like most about my job. Taking risks and making mistakes can lead to really great inventions. CarbonX is the proof!'
‘Thanks in part to InnovationQuarter, we were soon able to compete with the big players.’
Rutger van Raalten, CarbonX
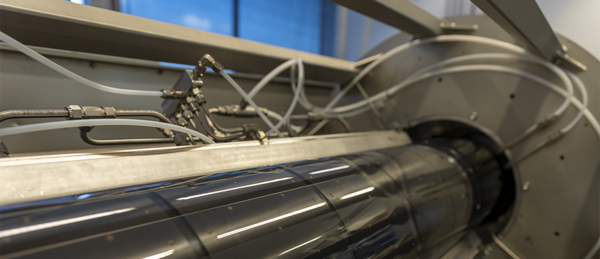
Kalpana Systems: ultra-thin layers for super-efficient batteries
CEO Diederick Spee once did a PhD on research into barriers to flexible electronics in the solar cell industry, among others. Years later, more or less by accident, he came up with a solution to what seemed at the time a fundamental problem: a machine that makes batteries as efficient and cheap as possible. His idea resonated, a patent was filed and Kalpana Systems was born.
From battery to beverage packaging
The company developed ‘an innovative machine that enables fast and cost-effective production of high-efficiency energy solutions, such as batteries, using sALD’. Spatial Atomic Layer Deposition, as it is called in full, deposits ultra-thin, extremely stable and uniform film layers on even the most complex 3D structures at low temperatures. This creates a chemically inert solid-electrolyte interface (SEI), allowing the battery to charge quickly and safely without shortening its lifetime. Kalpana was the first to realise a commercially viable production method for these stable and safe battery components. And it doesn't stop there: ‘The technology is usable and scalable in a wide range of industries, for example in solar panels, beverage and food packaging.’
Potential immediately clear
InnovationQuarter saw the potential immediately: ‘They were the first independent party to have confidence in us and were willing to put their money where their mouth was. It was a bold step for an investor.' And the cooperation with InnovationQuarter has been successful not only financially. 'They are incredibly proactive and know the playing field here in Zuid-Holland, but also beyond. Their network is huge and we make grateful use of it.'
‘The technology is usable and scalable in all kinds of industries, for example in solar panels, beverage and food packaging.’
Diederick Spee, Kalpana Systems